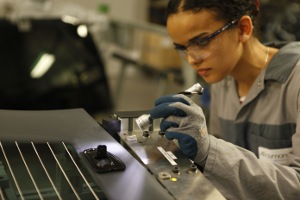
The brand's new concept car, presented at the Paris Motor Show, integrated an ARaymond™ innovative bonding solution.
Renault unveiled EOLAB, its new concept car, at the Paris Motor Show. This concept car is intended to preview the 2020 vehicle and incorporates technological building blocks, which should ultimately be included in the production vehicles. Main objective for those innovations: reducing C02 emissions in line with evolving environmental standards. Through this partnership, ARaymond and Renault demonstrate the ability of industrialists to work together in order to bring about future innovations.
EOLAB is a true laboratory for cars of the very near future. One of its goals was to bring together innovations that can be incorporated into future vehicles, to test them and to evaluate their ability to be easily integrated into production processes, within the existing Renault plants.
Among the technical challenges that the teams faced, the issue of vehicle weight is strategic: the lighter the vehicle, the lower are the CO2 emissions. One of the solutions for reducing vehicle weight was to use 4 lightweight materials: composite carbon or glass fiber, magnesium, aluminum and lightweight steel. However, these materials raise questions concerning their assembly: they are impossible to weld, often difficult to drill and their juxtaposition can lead to corrosion issues. Fastening by adhesive bonding seems to be the most relevant solution, notably for certain attachment points where traditional mechanical solutions cannot be considered.
The assembly experts from Renault were the first to recommend the ARaymond™ Bonding Solutions to the prototype fabrication manager, Philippe Moutardier, after having conducted comparative technical tests on multiple potential solutions and evaluating their performance. ARaymond offers an adhesive bonding technology for fasteners that utilizes an adhesive that is dry and tack free, clean to work with, developed for industrial automation. It enables instant tack (green strength) with load bearing capabilities (assembly) after just a few minutes.
Beyond the technical performance, the innovation provided by ARaymond lies also in the capability of developing the wholebonding solutions and in the design and implementation of full processes: they are not just providing a technology, but adding to that a very high level of support and customer project involvement at every stage. Thus, in a partnership approach, ARaymond invests in the development of the bonding solution, in defining the specifications, in the industrial implementation but goes well beyond that into the monitoring of the solution for future productions. Providing services is a pillar of ARaymond™ Bonding Solutions offer. It enhances performance and the efficiency of cooperation. It guides innovation as well as the quest for technical excellence. The management of customer issues is complete. This particular approach secures the bonding project, which results in a reduced overall budget for the customer, and generally distinguishes them from their competitors.
The final criterion is that of possible cooperation in the future, linked to the industrial integration capability of the innovation building blocks contained within "EOLAB". On this point, ARaymondoffer also made the difference, explains Valérie Coquereaux, Marketing Manager for the ARaymond™ bonding solutions: "Our added value lies in our ability to provide our customers with a very high level of technical expertise, but to also go well beyond, by providing a comprehensive range of services, all the way from the start of the project until the end. This is what sets our offer apart: to provide not only the technical solution, but to ensure that our customer can take ownership and fully integrate the solution with a very high level of support until the very last day of production. We are especially proud to have participated in the development of EOLAB, which is an excellent example of what two industrial companies can accomplish by working together in this particular way. This demonstrates that integrating an offer for a full range of services with industrial expertise allows for distinction within the market."
To learn more: www.araymond-automotive.com
See an excerpt of the interview on video.
About ARaymond Network
The ARaymond Network** is a worldwide leader in fastening and assembly solutions for the automotive industry, and has over recent years transferred its expertise and skills to new markets: TRUCK, INDUSTRIAL, ENERGIES, AGRICULTURE, and LIFE. A family business established in 1865, innovation has always been at the core of the ARaymond Network DNA, with its press-stud, a small assembly, now used worldwide. Today the ARaymond Network comprises 37 companies across four continents, with 11 design offices and 22 production sites. Six per cent of turnover is invested in research and development every year.
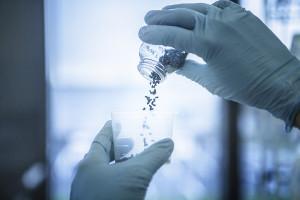
ADDITIONAL TECHNICAL INFORMATION:
Problem linked to the use of new materials in automobiles: the fastening!
- Conventional steel vehicle: the fastening is achieved through welding or drilling (we place a clip to accomplish the fastening)
- The new lightweight materials cannot be welded (even lightweight steel, when it is too thin)
- These new materials are not easy to drill:
- Composites: this destroys the network of fibers and damages the integrity of the material (weakens)
- Aluminum / Magnesium: corrosion issues when using a metal fastener
Therefore, bonding is a solution to the assembly problems encountered with lightweight materials.
- These Solutions are a range of services offered, relating to assembly through bonding issues
- These Solutions uses a specific adhesive, TechBond® PUR , associated with a particular process, Pick&Bond®
- It is an adhesive designed and developed by ARaymond.
- Dry and tack free (tablets or adhesive pellets)
- Easily distributed with a mechanical system
- Precisely positions the adhesive on the part to be bonded
- Possibility to apply a load to the bonded part right after bonding
- The Pick&Bond process was developed by ARaymond to be easily integrated into the production line at the OEMs or the manufacturers.
- The TechBond® PUR adhesive cures with heat
- The process steps are:
- Heat the part to be bonded
- "Pick" the adhesive (previously distributed)
- "Bond" on to the substrate
- Immediate hold
- We meet the industrial needs of our customers by successfully implementing a bonding solution and assisting throughout the project development and of the production life
- Our Services are based on:
- A unique adhesive technology and a particular bonding process which contribute to the fulfillment of our commitments
- A bonding project conducted with a specific methodology enables the mastery and control of all the elements which can affect the desired result
- A partnership: we coordinate the bonding project as a whole (up until the last day of production)
- Commitment to the desired results and billing based on the achievement of these results
- 2013: the team in charge of ARaymond™ Bonding Solutionsbegins a technical collaboration with RENAULT
- A series of bonding tests on composites and painted magnesium were conducted(upon the request of assembly expert, Mr. Philippe MICHEL (SDES Expert “Structural Bonding and Mechanical Deformation Assembly Processes” – DICAP)
- ARaymond bonding technique is chosen for its superior technical performance as compared to its competitors as well as for its ease of industrialization (automated bonding)
- End of 2013: RENAULT announces that ARaymond has been chosen to participate in the SUPER ALMA project within the framework of bonding fastening elements on to the concept car (later named EOLAB)
- Objective: to bond fastening elements (studs) on the carbon fiber floor panel and on the magnesium firewall (materials upon which welding or drilling is impossible)
- These studs enable the fastening of: heat shields (exhaust); cable channel, an underbody trim and pneumatic tubing for the assisted suspension
- Beginning of March 2014: TheARaymond team comes to the Renault “Technocentre” in order to bond, under industrial conditions, 45 studs on EOLAB: 35 on the chassis (exterior) and 10 on the interior of the vehicle (carbon fiber substrate and painted magnesium substrate)
- The bonding operation was performed in the Renault prototype workshop - the bonding was done manually but in an industrial manner in order to simulate assembly line usage (using an applicator – control of temperatures, activation time, and application)
- After March 2014: the vehicle was completed, fine-tuned and subjected to road tests
ARAYMOND™ is used as a trademark.
** “ARaymond Network” means a network of independent companies.